PCB Testing & Inspection
At Active-PCB Solutions, our rigorous PCB testing and inspection processes ensure that every assembly meets the highest standards before dispatch.
From functional testing to component placement verification, we use advanced technology to confirm that each printed circuit board performs flawlessly before it is delivered to you.
Automated Optical Inspection (AOI) & X-Ray Inspection
No product leaves Active-PCB without passing a rigorous inspection. We use advanced 3D Automated Optical Inspection (AOI) systems and X-ray equipment to meet the specific criteria set by our customers. These tools allow us to maintain the highest possible quality standards, ensuring that every product is inspected during production, repair, rework, and refurbishment.
Our in-house X-ray capabilities, featuring the Nordson-Dage Quadra 3 and Nordson-Dage XD7600NT system, enable us to detect hidden manufacturing internal structures and solder connection defects, checking every layer of the PCB without any risk of damage.
Every PCB is thoroughly inspected using our Koh Young Technology KSMART 3D Automated Optical Inspection (AOI) system with live data streaming, which tracks each board throughout the assembly process ensuring no defects go undetected. The quick error detection means that issues are spotted and corrected instantly, resulting in faster turnaround times and enhanced product quality.
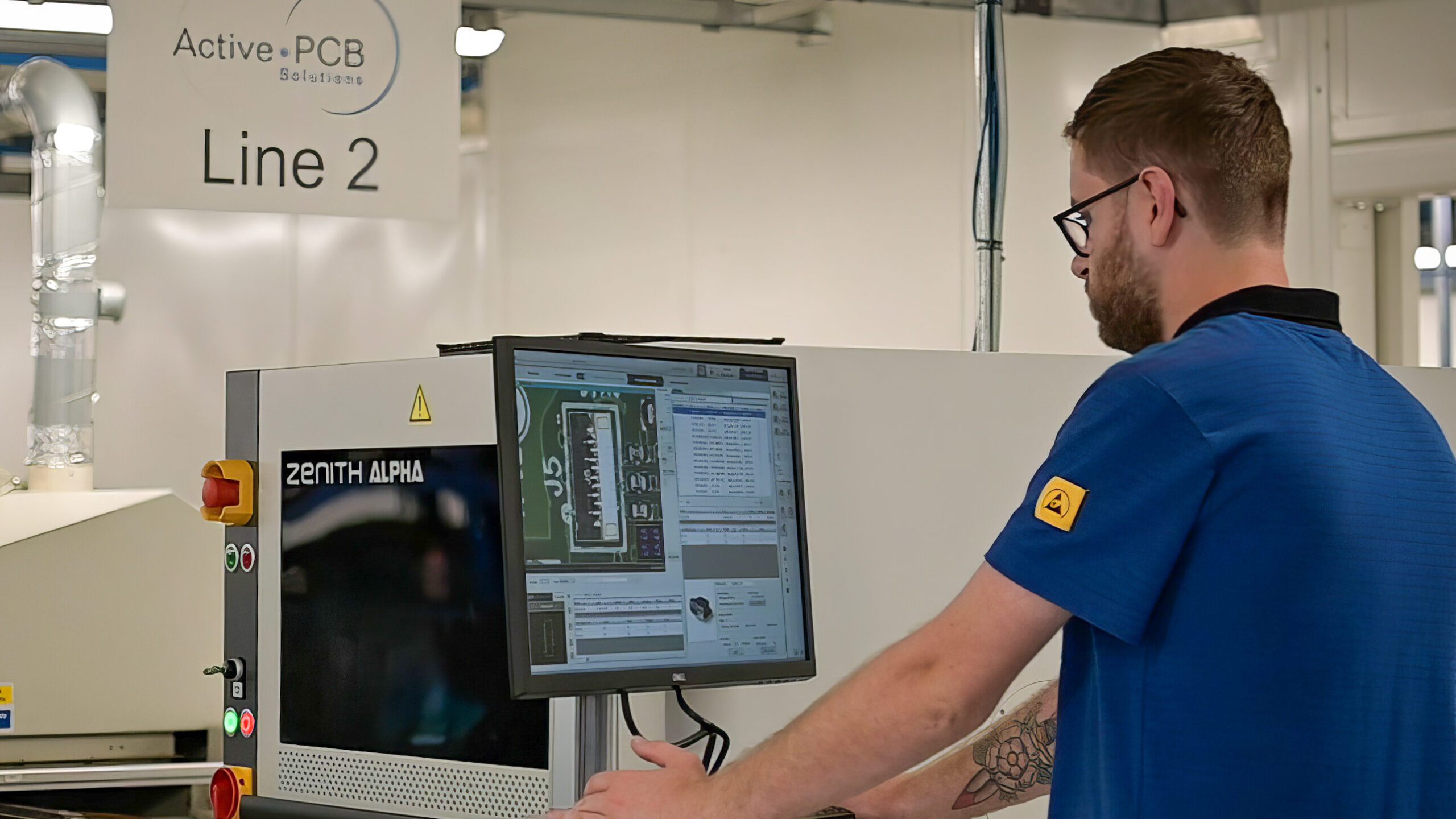
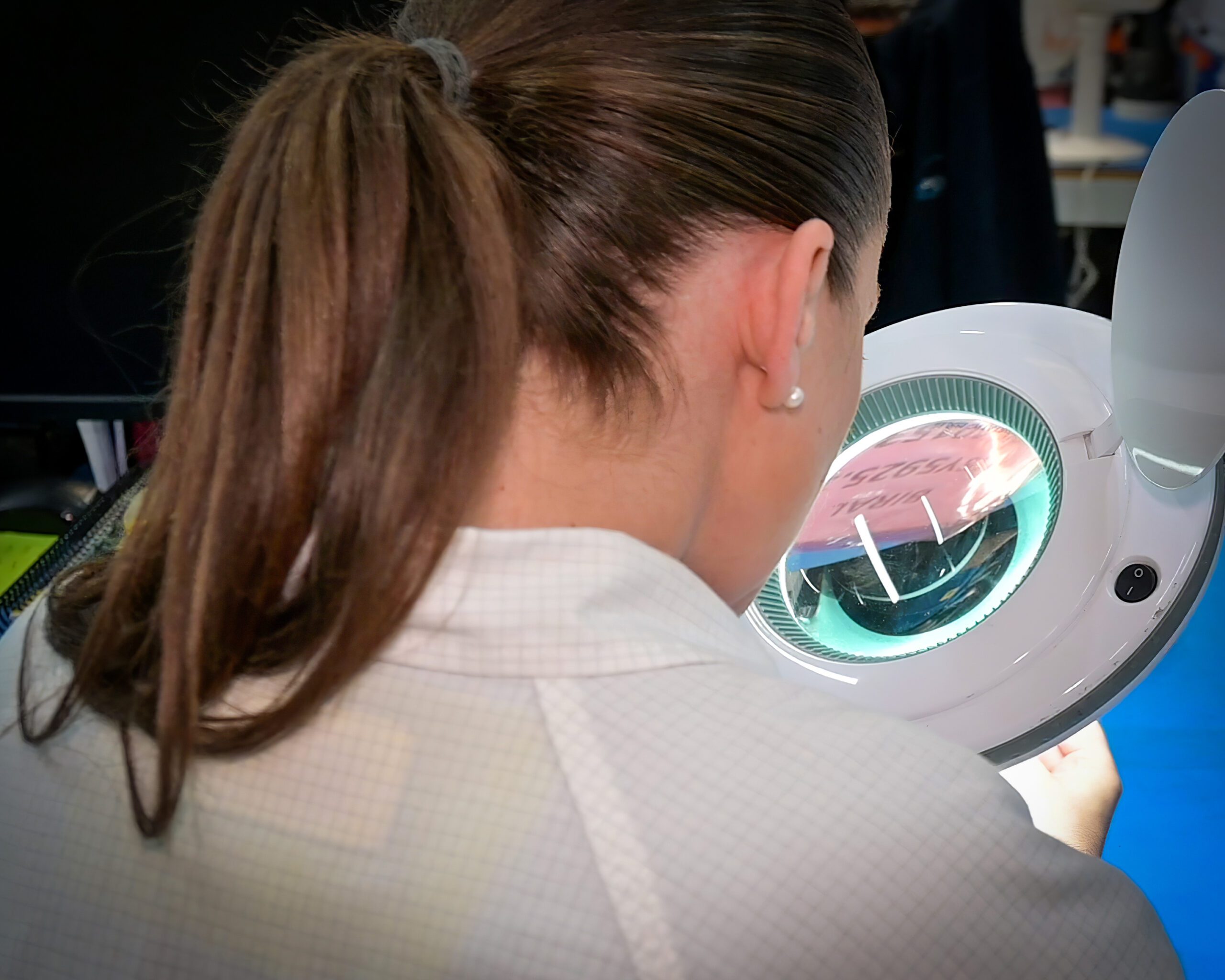
Manual Visual Inspection
Complementing our automated processes, our IPC-A610 trained quality inspectors perform detailed visual PCB inspections using the Vision Engineering Mantis magnification system, ensuring that even the smallest components meet our high standards.
Functional PCB Testing
Active-PCB Solutions offers a full suite of functional PCB testing capabilities, including Flying Probe Testing, in-circuit and off-circuit programming including boundary scan, PAT and HI-POT testing. These tests ensure that every assembly that leaves our factory performs perfectly.
We also use environmental stress screening to identify potential failures early by simulating extreme operational conditions, to make sure that your products work exactly as expected when they need to.
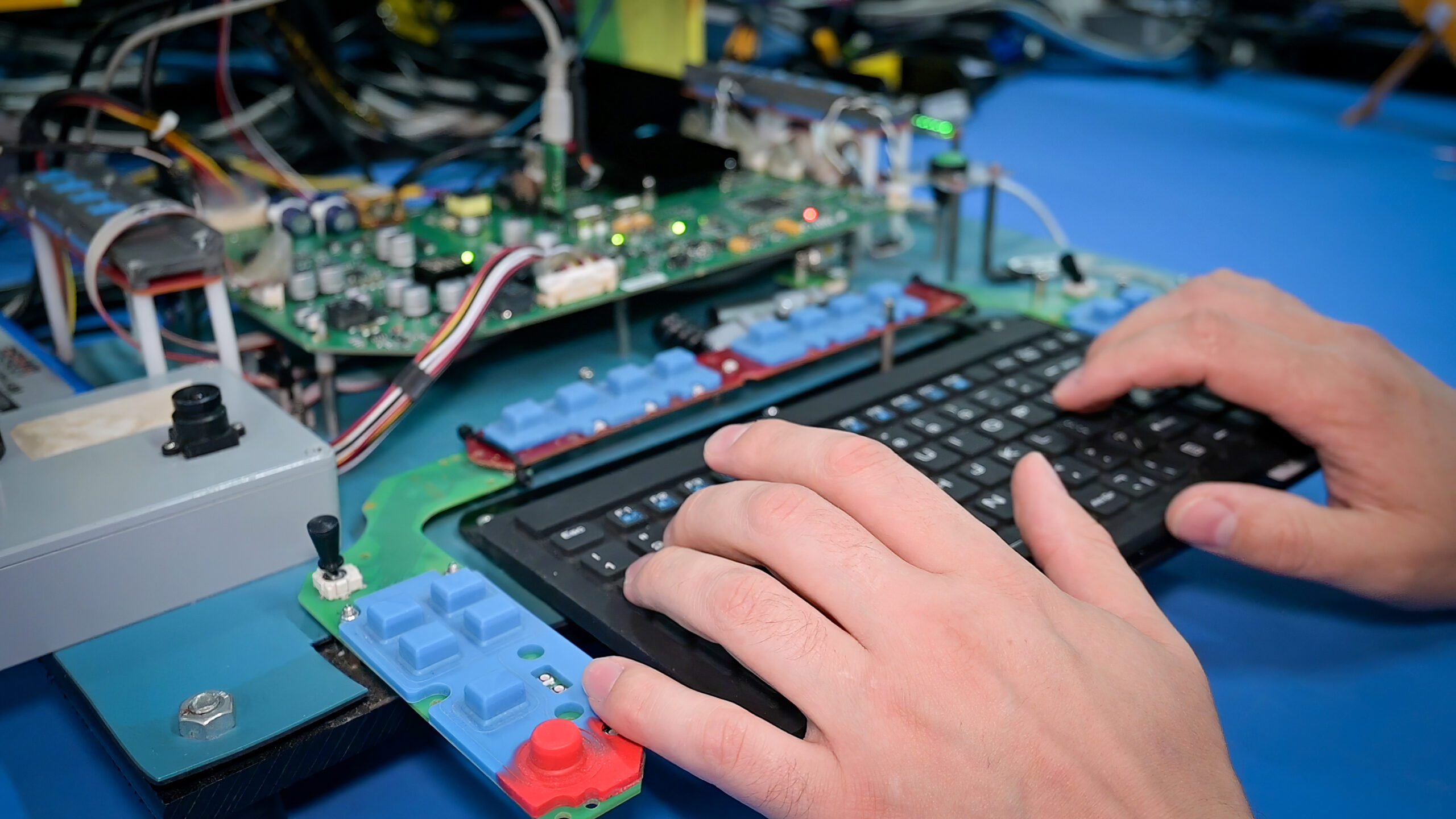