Printed Circuit Boards (PCBs) form the backbone of modern electronic devices, enabling the interconnection of components in a compact and reliable manner. Whether you’re developing cutting-edge consumer electronics or sophisticated industrial equipment, PCB prototyping and New Product Introduction (NPI) are critical steps in the product development lifecycle.
This quick guide to prototyping and NPI explains the journey from concept to production.
What is PCB Prototyping?
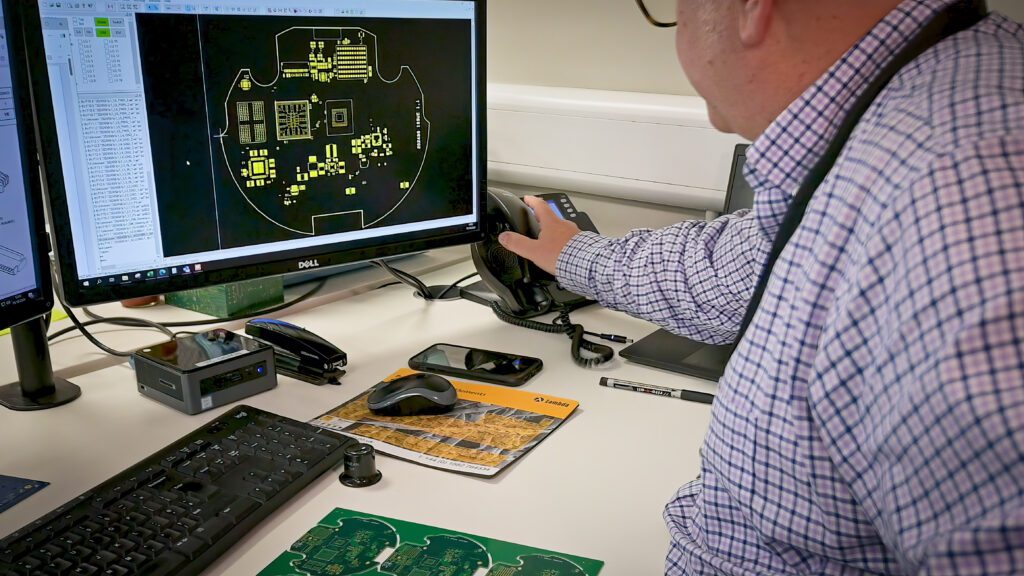
PCB prototyping involves creating a preliminary version of a circuit board so that it’s possible to test its functionality, design integrity, and performance before going into full-scale production.
This stage is essential for identifying potential design flaws which might not be picked up in the design, which saves time and wasted resources.
Key Steps in PCB Prototyping:
- Design Creation: Using Electronic Design Automation (EDA) tools, engineers design the schematic and layout of the PCB.
- Fabrication: A prototype board is manufactured based on the design specifications, including layer count, material selection, and trace layout.
- Assembly: Components are soldered onto the board using through hole or Surface Mount Technology to create a working prototype.
- Testing and Debugging: The prototype is subjected to various tests to verify functionality, signal integrity, and compliance with industry standards.
Understanding New Product Introduction (NPI)
NPI is the process of transitioning a product from the design phase into manufacturing.
For electronics, this involves integrating PCB production into a broader product development strategy.
Benefits of Effective PCB Prototyping and NPI
- Risk Reduction: Early detection of design flaws prevents costly mistakes during mass production.
- Improved Performance: Iterative testing ensures that the PCB meets performance standards and design specifications.
- Faster Time-to-Market: Streamlined prototyping and NPI processes accelerate the transition from concept to commercial product.
- Cost Efficiency: Optimising designs prior to manufacturing reduces waste and minimises production costs.
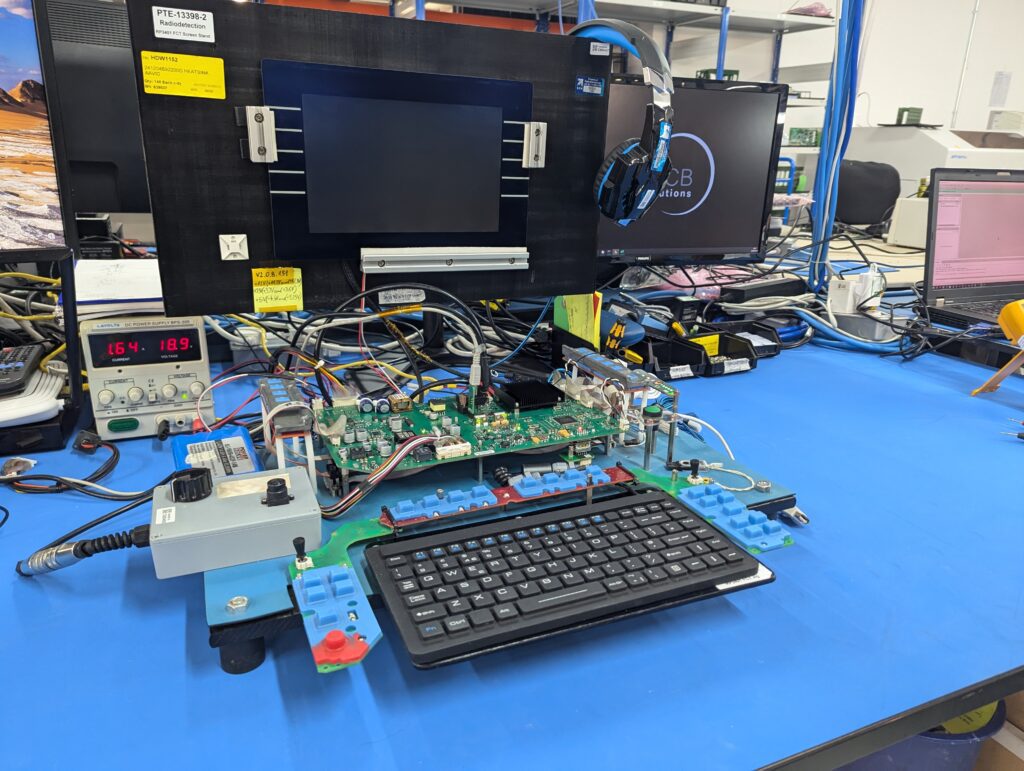
Best Practices for PCB Prototyping and NPI
- Start with a Clear Specification: Clearly define the product requirements, including functionality, size constraints, and environmental considerations.
- Invest in High-Quality Prototyping: Partner with experienced an experienced PCB manufacturer who can deliver accurate and reliable prototypes.
- Iterate and Validate: Don’t rush the process; use multiple prototype iterations to refine the design.
- Leverage Automation Tools: Use EDA software and simulation tools to minimise manual errors and optimise designs.
- Collaborate Across Teams: Foster communication between design, manufacturing, and quality assurance teams to address potential issues early.
Ready to bring your electronic innovation to life? Contact us at Active-PCB to explore how we can support your PCB prototyping and NPI needs.