PCB Assembly: Through-Hole & SMT
At Active PCB, we specialise in high-quality PCB assembly services, offering both Through-Hole Assembly and Surface Mount Technology (SMT) to meet the diverse manufacturing needs of our clients.
Our Through-Hole Assembly process ensures strong mechanical bonds and durability, making it ideal for applications in aerospace, automotive, and industrial sectors. Using advanced soldering techniques, we guarantee high reliability and precision in every assembled board.
For modern, high-density designs, our Surface Mount Technology (SMT) capabilities enable efficient, compact, and lightweight assemblies. With state-of-the-art equipment, we ensure precise component placement, effective soldering, and rigorous quality control to meet industry standards.
Through-Hole Assembly | Active-PCB Solutions
Plated or Pin Through-Hole Assembly (PTH) is a traditional PCB assembly technique where component leads are inserted into pre-drilled holes on the PCB, and then soldered to pads on the opposite side, either by a machine or hand soldered. This method creates strong mechanical bonds between components and the board, making it highly suitable for applications that endure substantial physical stress or high temperatures.
We offer a range of conventional Through-Hole PCB assembly services, including flow soldering, selective soldering, and precision hand soldering.
Automated insertion and other specialist equipment ensure high productivity while maintaining superior quality standards.
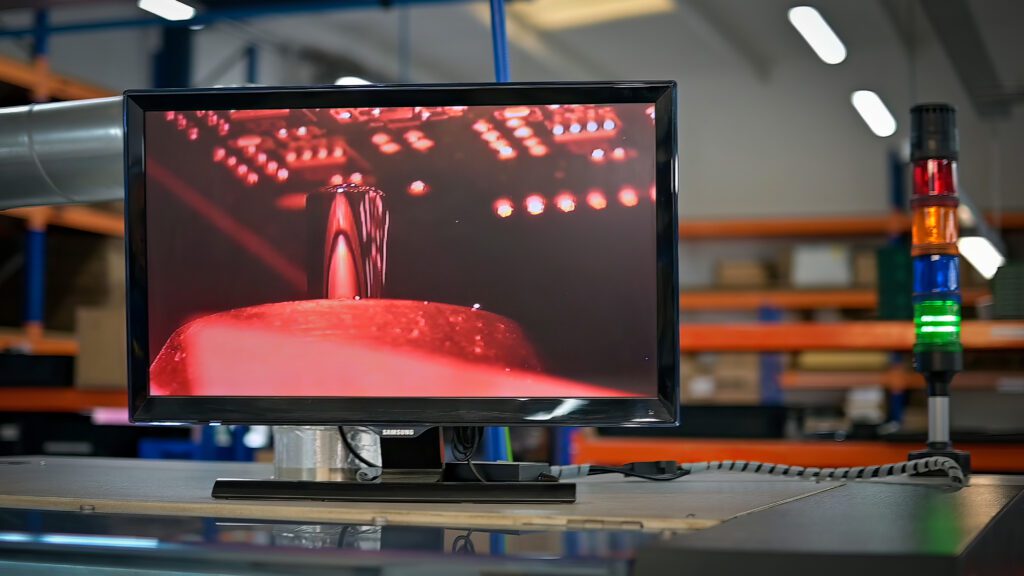
Benefits of Through-Hole Assembly
- Strength and Durability: The soldered PTH connections provide a sturdy, reliable bond, ensuring long-lasting component stability even under rigorous conditions.
- Prototyping and Testing: Due to its robustness and ease of handling, through-hole assembly is often used for prototypes and testing.
- Superior Heat Resistance: Through-hole components can often handle higher power loads, making this method ideal for industrial, automotive, and aerospace applications.
- Vital for Sensitive Components: Heat sensitive components and batteries cannot go through the wave soldering or SMT machines so, need to be hand soldered using through-hole assembly.
Drawbacks of Through-Hole Assembly:
- Space and Weight Limitations: Through-hole assembly is bulkier, with components protruding through the PCB, which may not be suitable for high-density, compact designs.
- Slower Assembly Time: The additional drilling and manual or wave soldering required make this a more time-consuming and costly process, especially for high-volume production.
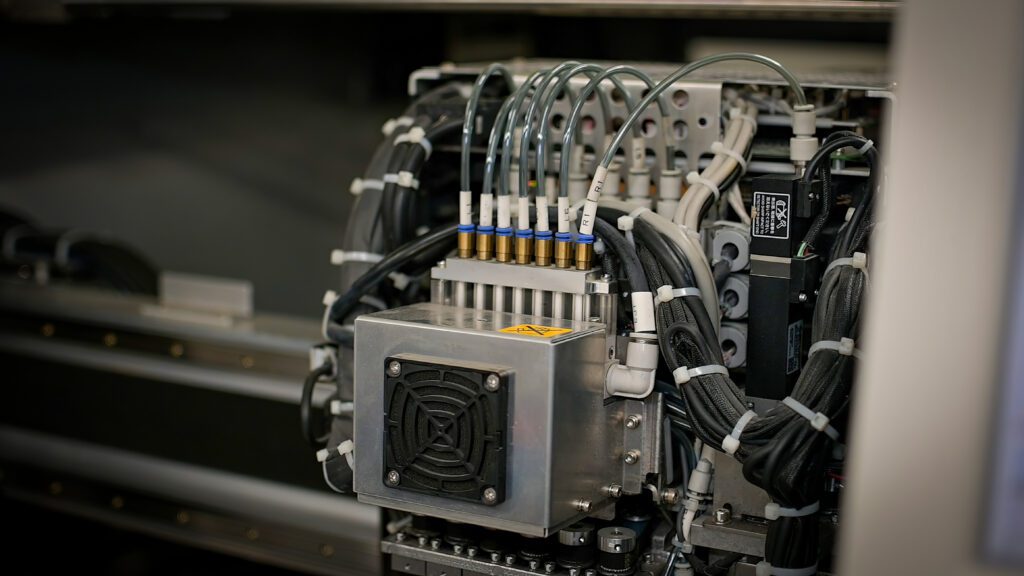
Surface Mount Technology (SMT) | Active-PCB Solutions
Surface Mount Technology (SMT) is a more modern PCB assembly method in which components are placed directly onto the PCB surface without the need for holes. SMT allows for smaller, lighter, and more complex assemblies, making it ideal for high-density designs, particularly in consumer electronics and telecommunications.
Our advanced SMT assembly services are powered by Juki placement machines, DEK screen printers, and BTU reflow ovens.
Whether working with 01005 packages, BGAs, QFNs, or flip-chip technologies, we can offer scalable solutions from prototyping to high-volume production.
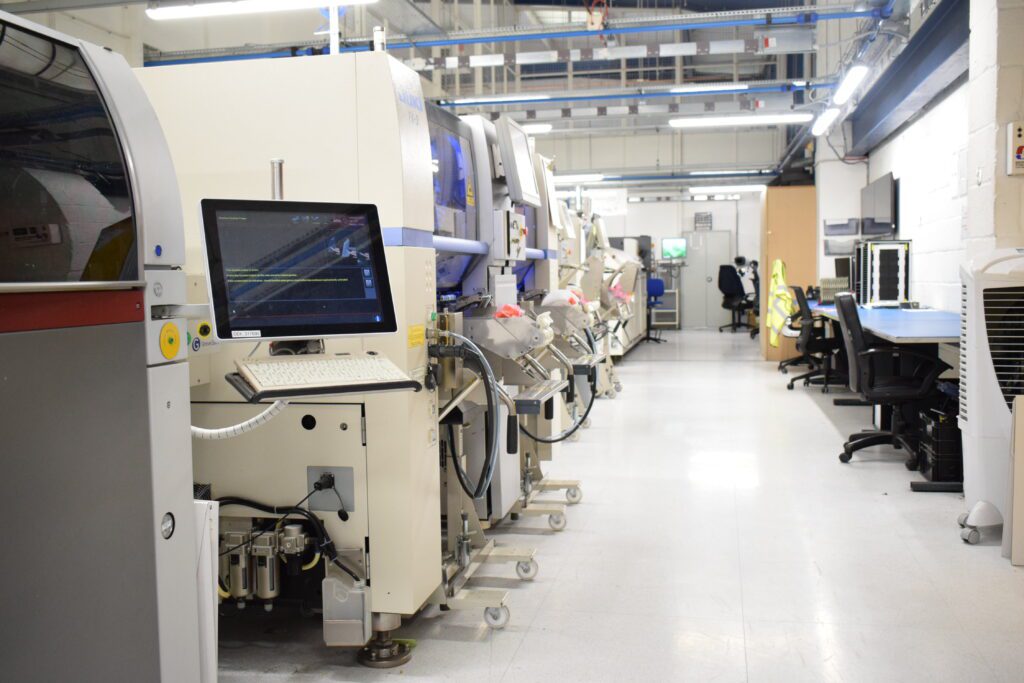
Benefits of SMT:
- Compact and Lightweight: Surface Mount Technology components are much smaller, which allows for greater component density and enables lightweight, more compact device designs.
- Faster Assembly Process: SMT utilises automated equipment to place and solder components, resulting in higher production speed and efficiency, particularly beneficial for large-scale production.
- Automated Optical Inspection: PCBs can be inspected straight off the SMT line by our advanced AOI machinery, which detects errors in real time and means that these can be rectified even mid-run to save time and increase efficiency and quality.
- Design Flexibility: The smaller size and versatility of SMT components allow engineers to achieve complex circuit designs on limited board space.
Drawbacks of SMT:
- Reduced Mechanical Strength: SMT does not offer the same mechanical durability as through-hole mounting, as the components are only soldered to the surface pads, which can limit its suitability in high-stress environments.
- Thermal and Power Limitations: SMT components may not handle high power levels as effectively as through-hole components, limiting their use in certain heavy-duty or high-temperature applications.
- Component limitations: Due to the high heat of the reflow ovens, SMT assembly is not appropriate for heat sensitive components or batteries.
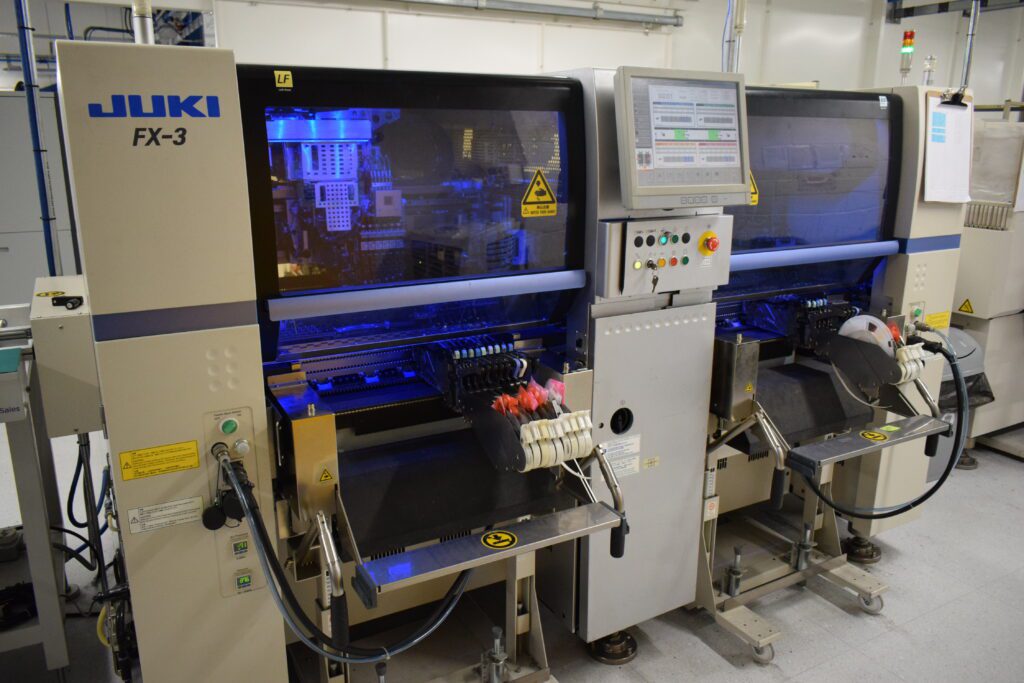
Comparing Through-Hole Assembly and SMT
When choosing between through-hole assembly and SMT for assembling printed circuit boards, it’s important to consider the intended application, design requirements, and production volume.
Whereas pin through-hole assembly offers durability and reliability, particularly for devices subjected to high mechanical stress or extreme conditions, for compact, lightweight designs that demand higher circuit complexity and production speed, SMT is the preferred choice due to its space-saving and automation-friendly properties.
In most modern PCB assemblies, a combination of PTH and SMT assemblies will be used to achieve a flawless printed circuit board.
At Active-PCB, we support both through-hole and SMT assembly, ensuring that our clients receive the best solution for their unique project needs. Whether you prioritise strength, compactness, speed, or flexibility, our team is here to guide you through selecting the best assembly method to achieve high-quality, efficient, and reliable results.