Functional Testing
Functional testing of PCBs is an essential step in the production process of printed circuit boards (PCBs) that ensures every board we produce performs exactly as intended in its end application.
At Active-PCB Solutions, we know the importance of quality and reliability in electronic assemblies, and our functional testing services are tailored to verify that each PCB meets your required operational specifications.
Functional Testing for Printed Circuit Boards | Active-PCB Solutions
Functional testing is conducted after the assembly of the PCB. Unlike other testing methods that might only check for continuity or basic component placement, these tests ensure the board operates under specific simulated conditions, mirroring its real-world use case as closely as possible. The purpose is to validate the functionality of the board’s design by replicating its operational environment.
Each board is tested by our team of trained testers according to its defined functions, which could include signal processing, power distribution, communication protocols, or any other functions that the board is designed to handle.
Why Functional Testing of PCBs is Critical
Functional testing of PCBs allows manufacturers to detect and correct defects at an early stage, before they escalate into larger production or customer-reported issues.
This testing phase verifies:
- System Performance: We make sure that each printed circuit board meets its performance specifications under typical operating conditions.
- Component Reliability: The tests will pick up potential failures in individual components that may impact overall performance.
- End-User Functionality: The board performs as expected from an end-user perspective, whether it’s powering a sensor, managing power supply, or interfacing with other components in a complex assembly.
Early detection of any defects can significantly reduce the risk of costly rework or customer returns, while enhancing product reliability and overall quality.
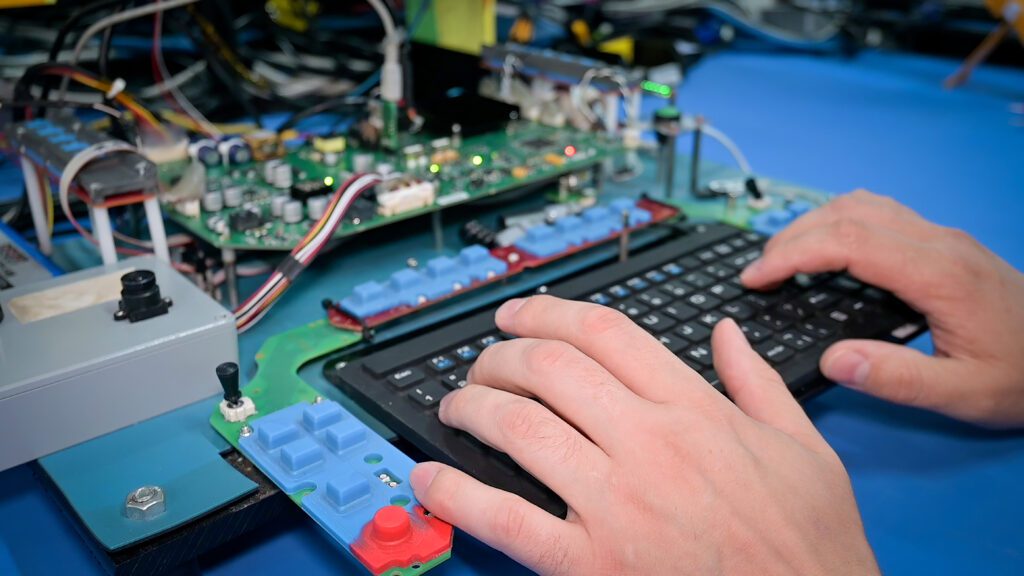
Our Functional Testing Process
- Test Development: Our experienced engineers work with you to understand the functional requirements of your PCB – i.e. what it is designed to do in its real-world application – and develop a tailored testing protocol. This may involve creating custom test jigs, adapters, or test software.
- Simulation of Real-World Conditions: We simulate the operational environment of the board, including power cycling, temperature variations, and loads it would typically encounter, so you can be confident that it will work as it’s supposed to.
- Signal and Communication Verification: For PCBs that utilise specific communication protocols (e.g., I2C, UART, SPI), we confirm data transfer, signal integrity, and timing compliance.
Advantages of Functional Testing with Active-PCB Solutions
- Customised Testing Solutions: We adapt our testing to your specific board requirements, which can range from basic power-on checks to advanced, fully automated testing setups.
- Experienced Technicians and Engineers: Our team are highly trained and all team members have extensive knowledge in PCB assembly and testing, allowing us to provide high-quality, reliable testing services.
- Quality Assurance: Functional testing of PCBs at Active-PCB aligns and often surpasses industry standards, helping ensure that each circuit board we deliver meets or exceeds customers’ high expectations for reliability and performance.
Contact Us
For more information on our functional testing services or to discuss your project, please contact us today. Let Active-PCB be your partner in achieving unmatched product quality and reliability.