At Active-PCB Solutions, we are always looking for ways to improve our manufacturing processes and ensure that only the highest quality products make it out of the door and to our customers. That’s why we’re excited to introduce a significant upgrade to our Surface Mount Technology (SMT) line: a brand-new conveyor and buffering/stacking system which was installed last week.
This enhancement is set to streamline our operations, reducing the need for manual handling of printed circuit boards (PCBs) and making our process smoother than ever before.
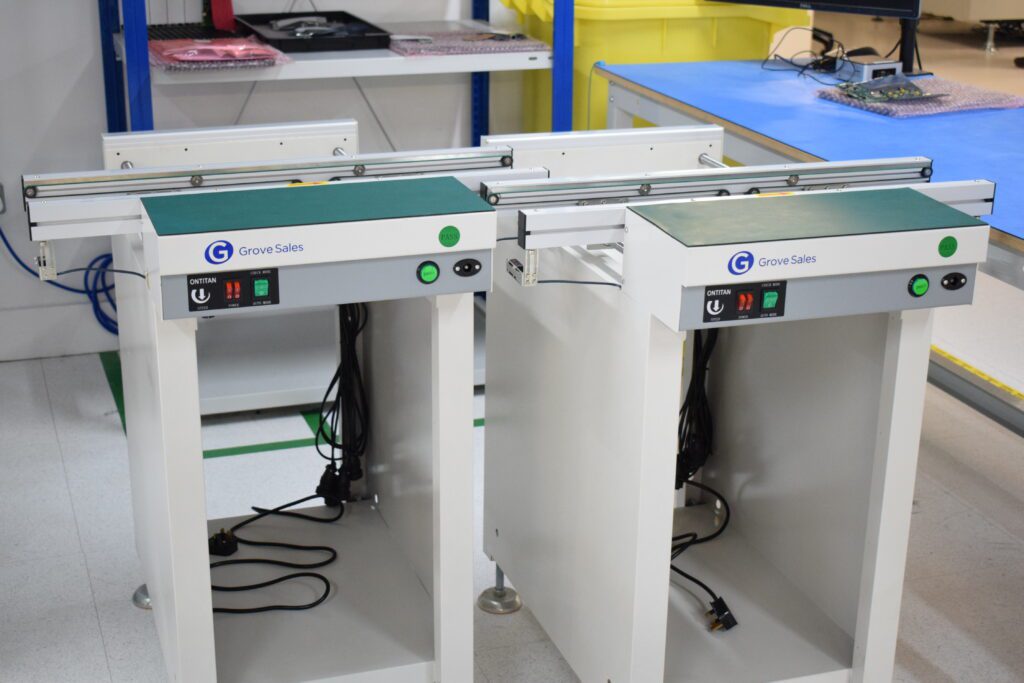
Less Handling, More Efficiency
One of the key benefits of our new conveyor and buffering system is the reduction in manual PCB handling. Previously, operators had to frequently load and unload PCBs at different stages of production, increasing the risk of damage, misalignment, and production bottlenecks.
With our new system in place, PCBs move seamlessly from the reflow oven to be inspected by the Koh Young AOI machine with no need for human intervention.
This not only improves efficiency, but also enhances the consistency of our manufacturing process by taking out any risk of human error.
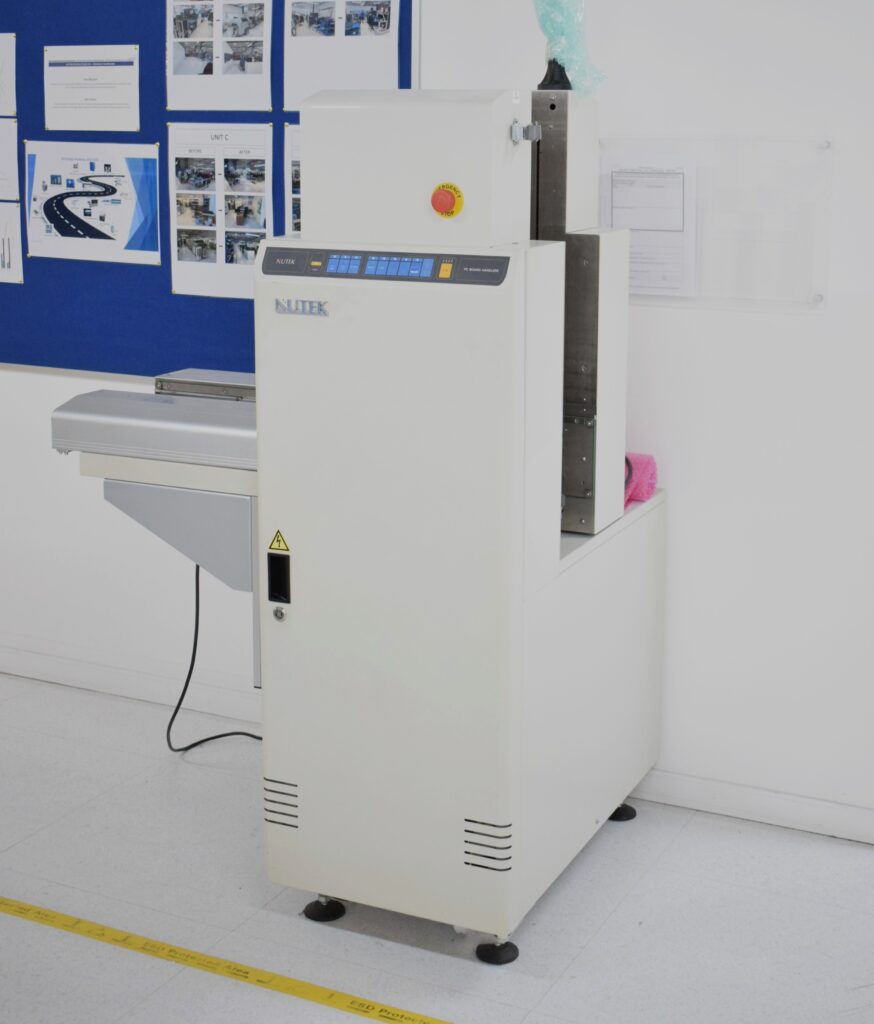
Reducing Production Bottlenecks
Our new conveyor and buffering/stacking system ensures that PCBs are properly queued and ready for the next step in the production process. This prevents delays caused by inconsistencies in PCB flow and ensures that every board progresses smoothly through the SMT line. By eliminating unnecessary pauses and interruptions, we can achieve higher throughput and maintain steady production rates.
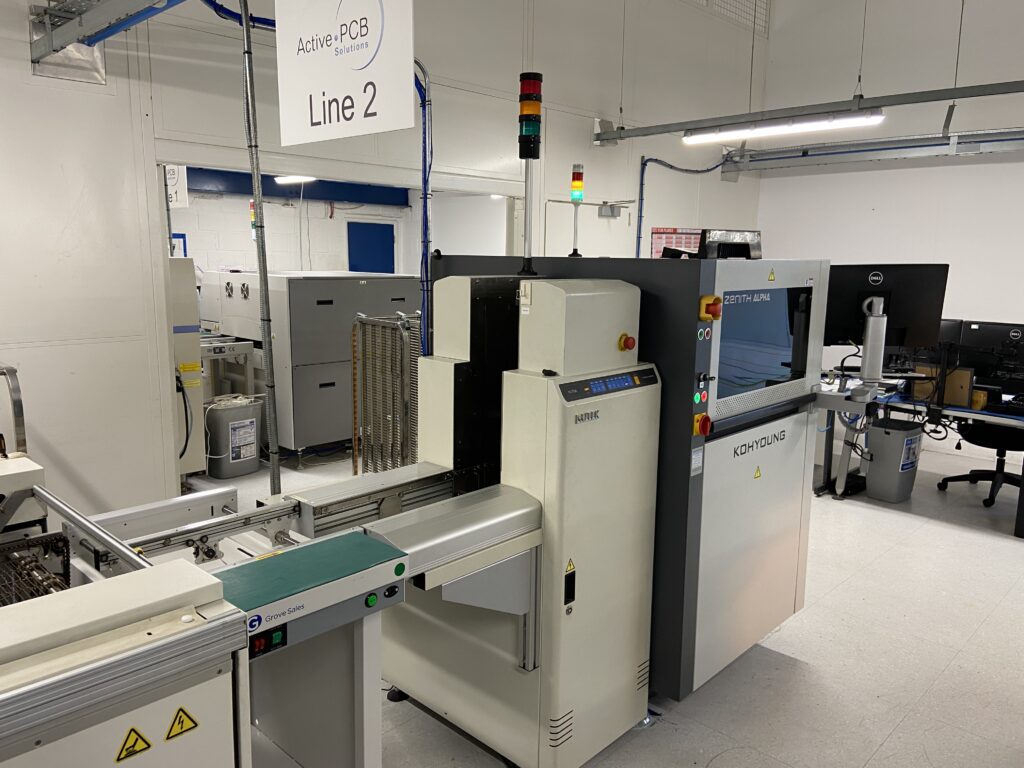
Improving Quality and Reliability
Each time a PCB is handled manually, there is a potential risk of contamination, misplacement, or damage. Less manual handling therefore means fewer opportunities for human error to occur.
By automating the movement of PCBs through the entire SMT line from component placement to inspection, we reduce these risks, leading to a more reliable and high-quality end product. Additionally, the improved flow control helps maintain optimal working conditions for each component placed on the board.
Enhancing Workplace Efficiency and Operator Focus
By reducing the need for constant manual intervention, our team can focus on more critical tasks such as quality control, machine maintenance, and process optimisation.
This not only improves productivity but also makes for a better working environment where operators can dedicate their time and expertise to ensuring the best possible results.
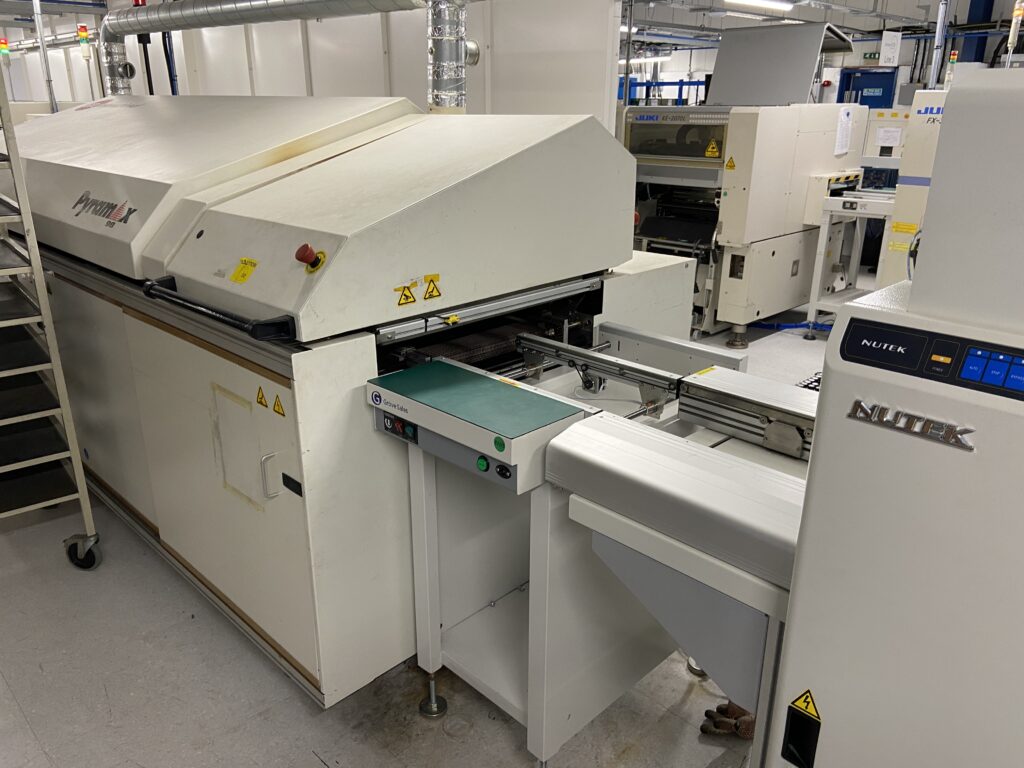
Looking Ahead
The installation of our new conveyor and buffering/stacking system is just one of many steps we’re taking to optimise our SMT line.
As we continue to invest in automation and efficiency improvements, we remain committed to providing our customers with flawless products while maintaining a smooth, streamlined production process.
We’re excited about the positive impact this upgrade will have on our operations, and we look forward to sharing more innovations in the future as part of our commitment to continuous improvement.
Stay tuned for further enhancements as we strive to make our SMT PCB assembly line even more efficient and reliable.